7 Must-Know Manufacturing Trends For 2025
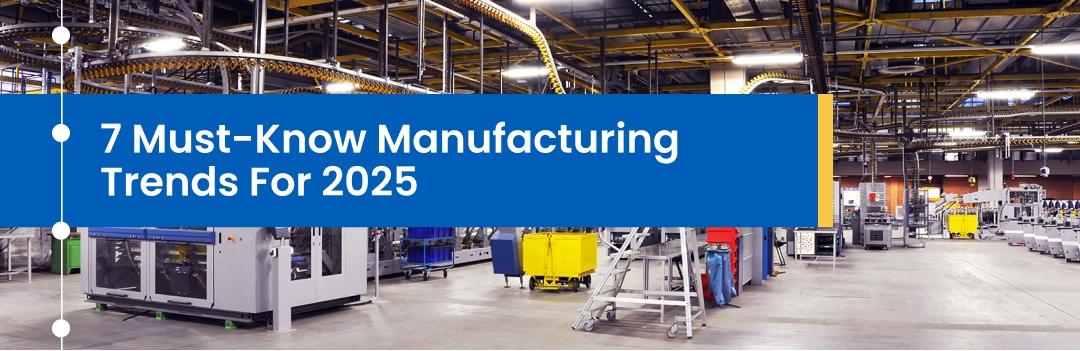
The year 2025 is shaping up to be one that brings transformative trends in the manufacturing industry. From AI-driven decision-making to predictive analytics - technology-powered trends are all set to make sweeping changes in the way manufacturing businesses thrive and function.
If you want to stay ahead of the curve, it is imperative that your business adopts and adapts to these changes. At least the ones that make the most sense for your business.
In this blog, we’ve compiled a list of the most useful manufacturing trends for 2025 so you’ll be better armed with the knowledge of future-proofing techniques in store for your business. Needless to say, custom manufacturing software is one of them, so let’s dive right in!
1. IoT - Internet of Things
Some trends keep coming back (or perhaps they never leave?). The internet of things is just one of them and it is set to grow even bigger in the year 2025! That said, when it comes to the role of IoT in manufacturing, it is important to keep certain stats in mind.
For example, as per IoT Analytics’ Summer Report 2024, the number of devices connected to the internet was supposed to hit 18.8 billion by the end of last year. In fact, by 2030, the world is expected to have 40 billion IoT devices as per the same report!
How does that translate to manufacturing? By taking your business online, you can leverage real-time data to make prompt and well-informed decisions that are poised for growth. That’s not all. It can also help you improve the efficiency of your entire manufacturing process, which can further help you bring down operational costs. That’s the power of leveraging smart devices for manufacturing!
2. B2B to B2C Transition
Consumer behavior can be very dynamic and highly influential, leading to significant shifts in business models. For 2025, that shift signals a transition from a B2B to a B2C business model for many manufacturing businesses.
The reason for this shift can be attributed to the many benefits a B2C model brings - from a higher profit margin to a faster entry into the market. Businesses also get the opportunity to improve their pricing, offer a wider selection of products, get prompt customer feedback and much more - all of which can help enterprises devise solid strategies for growth.
Of course, such a major transition can be cumbersome to carry out. However, with the help of custom manufacturing software, it can be relatively easier to make the switch or balance both without leading to issues such as data loss, data overlap and the like.
3. Predictive Analytics & Maintenance
As a manufacturer, you know that your business can be susceptible to losses in certain scenarios. Disruption in production schedules, machine downtime, volatility of demand and other such factors can lead to heavy losses that can be avoided with comprehensive manufacturing software solutions.
Allow us to explain. Custom manufacturing software can be equipped with predictive analytic tools that will analyze your business’s operations to provide you with real-time data that can be used to optimize the production process.
For example, with predictive analytics you can monitor the health of your manufacturing machinery. Key insights from this analysis can help you prevent unplanned downtime by promptly detecting potential issues before they turn into a major problem. Technicians can use this data to carry out speedy maintenance and repair services.
There are other benefits to predictive analytics too. Cloud-based machine health monitoring gives you access to centralized data anytime, anywhere in the world. What’s more, the insights gained from predictive analytics can help you make informed data-backed decisions in a proactive manner.
Besides, prompt handling of issues before they become a problem not only helps cut your losses but can also be effective in boosting your company’s revenue.
4. ERP Manufacturing Systems
Enterprise Resource Planning or ERP has been no stranger to the manufacturing world. That said, it is bound to gain stronger momentum this year, turning into a necessity for manufacturing companies. Why? Because it can help you carry out multiple tasks with ease.
Custom ERP software plays a crucial role in streamlining operations, providing real-time actionable data and in reducing costs. In fact, taking a data-driven ERP approach can be very beneficial for your business provided you have certain tools in place such as:
- Cloud ERP
Cloud-based data storage has been around for a while but more manufacturing businesses are embracing it now than ever before. A cloud-based ERP system can make it very easy to move around large volumes of data. Plus, its cost-saving and customization options make it a top-draw among manufacturers of different shapes and sizes.
- Mobile ERP
When your workforce is mostly mobile (or remote or hybrid), you have to be mobile too. Providing your employees real-time access to vital company information or customer communications is key so they can promptly address any tasks at hand. Mobile ERP apps can make that much easier by offering its users multiple options - from creating events to sending new alerts, approving sales orders and much more.
5. Automation & Artificial Intelligence
Cutting-edge technologies have a role to play in the manufacturing process. Artificial intelligence, automation, machine learning as well as VR (virtual reality) can help manufacturers achieve new levels of efficiency by allowing processes such as remote monitoring, equipment operation as well as servicing.
A game-changer in its own right, such technology does not require operators and workers to be on-site, thus minimizing downtime to a great extent. Virtual and remote operations also give employees greater flexibility while ensuring worker safety. In fact, in 2025, it won’t be bizarre to find factories that are fully automated with no manual labor involved whatsoever!
Moreover, automation of other valuable processes such as order placement, processing, shipment and fulfillment can help manufacturers have an error-free streak when it comes to deliveries. Plus, automated reports can make it easier to track trends such as seasonality, peak periods and phases of low demand so you can adjust your inventories accordingly.
6. Data-Powered Maintenance
COVID lockdowns brought with them many hardships for manufacturing businesses, which they are still recovering from. Machine downtimes were common and carrying out maintenance work was a lot harder than it used to be. Although things are back to normal now, having the flexibility to carry out remote diagnostics has become the need of the hour.
That’s where data-driven maintenance comes in. From IoT devices to sensors as well as software that conduct remote monitoring, each of them serve as reliable modes of communication that collect and record data to help with predictive maintenance. They are highly effective in reducing unplanned downtime, leading to major cost-savings for businesses.
What’s more, with the 5G network taking over, manufacturers now have the bandwidth to speedily deliver important data in real-time to the central server. This can further reduce possible downtime by enabling swift action to resolve the identified issues. Consequently, such data-driven maintenance can help manufacturers optimize equipment performance, thus increasing its lifespan.
7. Cybersecurity
Finally, with more and more businesses relying on manufacturing software solutions to run their day-to-day, protection against cybercrime has gained momentum. While investing in good software can safeguard your systems and sensitive data, it is vital to be proactive when it comes to taking security measures.
Regularly conducting security audits along with advanced encryption of sensitive data, role-based employee access and AI-powered threat detection systems can help you detect anomalies and take strict action against them in real-time. This can save your company from data theft. Rigorous security measures can even prevent financial losses if strictly implemented.
Conclusion
Equipping your manufacturing business with the latest trends can help you overcome key challenges such as downtime and inefficiencies. To ensure you get the most out of these trends, it is crucial to implement manufacturing software solutions that have all the features you need. Vestra Inet has 20 years of experience in developing custom manufacturing software that is tailored to the unique demands of your business. Contact us today to get custom software with future-proof features and robust security.