Benefits of ERP in Manufacturing: How do Disconnected Systems Slow Your Production?
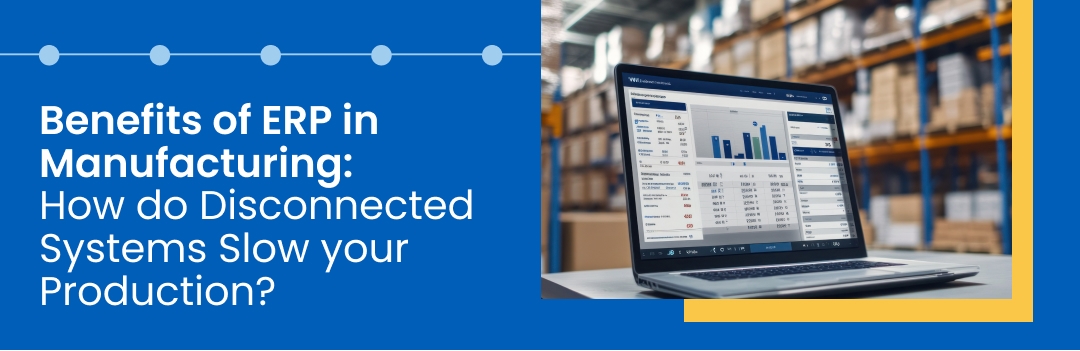
In today's highly competitive industrial environment, efficient operations in manufacturing are critical. However, disjointed systems can impede clarity and productivity by acting as a cacophony of instruments.
The instrument that unifies fragmented processes and propels your production force to a crescendo of success is custom ERP: Enterprise Resource Planning software.
This in-depth blog explores the benefits of ERP in manufacturing, showing how manufacturers may gain more control, increased productivity, and eventually a competitive edge with a single, integrated system.
Here, we'll examine the drawbacks of disjointed systems and reveal how a custom ERP solution can revolutionize an organization’s processes.
Challenges in Manufacturing Linked to Disconnected Systems
Let's examine the difficulties presented by disjointed systems before delving into the benefits of ERP in manufacturing.
Consider having customer information kept in a segregated CRM system, inventory levels monitored on some other software, and production data dispersed across spreadsheets. This disjointed strategy, while common, fosters mistakes, hold-ups, and poor visibility across the production process.
Disjointed systems can impede your output in the following ways:
Data Silos and Discrepancies
It is challenging to create a single source of truth in disconnected systems since they frequently result in data redundancy and inconsistency. For example, the purchasing and manufacturing divisions may have different inventory levels, which could result in shortages or overstocking.
If you do not utilize the benefits of ERP in manufacturing to overcome data silos you will end up with missed production deadlines, higher inventory expenses, and unhappy customers.
Ineffective Communication Among Systems
Information dissemination across several systems is error-prone and time-consuming. Communication breakdowns can cause missed deadlines, interfere with departmental cooperation, and upset production schedules. This lack of cooperation might raise expenses and affect overall productivity.
Limited Decision-Making and Visibility
When departmental visibility is restricted, it becomes difficult to recognize patterns, identify bottlenecks, and make wise production decisions.
For instance, production managers can find it difficult to modify production schedules promptly if they do not have access to real-time information on the amount of inventory or equipment downtime. Delays in production and missed delivery dates can arise from this.
Increased Delays and Errors
The manufacturing flow is further disrupted by human error that occurs when data is manually entered across systems. Inaccurate projections, erroneous computations, and manufacturing delays can result from data entry mistakes. Furthermore, manual procedures take a lot of time and are prone to errors, which might lower productivity.
These issues can considerably impact your bottom line. When managers do not realize the benefits of ERP in manufacturing, it can result in:
● Increased Production Costs: Your profitability can be greatly impacted by resource waste, high carrying costs for inventory, and production delays.
● Decreased Customer Satisfaction: Poor communication, late deliveries, and inconsistent quality can all have a detrimental effect on client loyalty and satisfaction.
● Limited Growth Potential: Your capacity to expand and adapt to changes in the market can be hampered by the difficulties presented by disjointed systems.
Benefits of ERP in Manufacturing
Simplifying Operations with Better Data Visibility
Real-time Data Availability
Production staff have access to real-time information on inventory levels, equipment use, and production progress thanks to a centralized database.
This gives them the ability to foresee possible problems in advance, modify production plans as needed, and make well-informed choices that maximize the use of available resources.
Improved customer satisfaction and production flexibility result from quicker reaction times to shifting demands.
Better Inventory Management
Custom ERP software makes it possible to have better control over inventory, which reduces overstocking and stockouts. Manufacturers can improve ordering plans based on fluctuations in demand and by having precise inventory insight across all locations.
It is one of the most crucial benefits of ERP in manufacturing, which guarantees that essential resources are always present to prevent production delays and lowers carrying costs related to surplus inventories.
Streamlined Production Planning & Control
Custom ERP systems streamline production planning by considering material availability, machine capacity, and lead times. This allows for the creation of realistic production schedules that consider all dependencies.
By ensuring on-time deliveries and minimizing production delays, manufacturers can maintain a consistent flow of goods and enhance customer confidence.
Efficient Material Requirements Planning
Automatic MRP calculation is one of the benefits of ERP in manufacturing that supports production by ensuring manufacturers have the right materials at the right time to meet production demands. This eliminates the need for manual calculations and minimizes the risk of errors.
MRP functionality allows for proactive purchasing and avoids production bottlenecks caused by material shortages.
Improved Quality Control
ERPs can be integrated with quality control procedures, enabling defect detection and real-time manufacturing process monitoring. This makes it possible to take prompt remedial action, reducing the production of defective items and the related rework expenses.
Manufacturers can gain consumers' confidence and brand loyalty by continuously producing high-quality goods.
Better Collaboration and Communication
Departmental collaboration is made easier with a single data source. The fact that all participants in the manufacturing process can view the same data promotes cooperation and guarantees that everyone is on the same page.
As a result, there are fewer breakdowns in communication, fewer mistakes, and a more productive and efficient manufacturing environment.
Significant cost reductions and increased competitiveness are some common benefits of ERP in manufacturing, which include better data visibility and optimized operations.
Manufacturers can make data-driven choices that optimize the allocation of resources, cut waste, and guarantee on-time delivery by obtaining a comprehensive view of their operations.
Reduced Expenses and Improved Efficiency
Decreased Errors and Waste
Outdated information and manual data entry lead to waste and errors. Simplified processes and real-time data visibility reduce the probability of such errors.
Custom ERP systems drastically lower the possibility of human mistakes by automating repetitive processes and eliminating the necessity for manual data entry.
Furthermore, real-time data guarantees that production choices are founded on up-to-date knowledge, reducing material and resource waste.
Enhanced Production Procedures
Manufacturers can locate bottlenecks and enhance production procedures for optimal effectiveness with the help of ERP software.
Custom ERP facilitates the implementation of process improvements by assisting managers in identifying areas where manufacturing slows down through data analysis.
Increased productivity and better use of resources lead to higher profit margins as a result of this optimization.
Decreased Manufacturing Costs
ERP systems help achieve substantial cost savings over time by reducing waste, streamlining manufacturing procedures, and enhancing inventory control.
The benefits of ERP in manufacturing go beyond production because better communication and more efficient processes can result in lower administrative expenses.
Manufacturers can increase their profitability and competitiveness in the market by reducing overall operating costs.
Better Use of Resources
ERP software assists producers in allocating resources as efficiently as possible, guaranteeing the effective use of labor, equipment, and materials.
This increases production and decreases idle time. Manufacturers can ensure a smooth and effective production flow by reallocating unused resources to regions with increased demand.
Faster Time-to-Market
ERP systems assist manufacturers in bringing products to market more quickly by optimizing workflows and cutting lead times. This is accomplished through quicker product development cycles, more effective material allocation, and better planning and scheduling.
Manufacturers who have a quicker time to market understand the benefits of ERP in manufacturing quite well. They take advantage of market opportunities and react swiftly to shifting consumer expectations.
Better Strategic Planning and Decision Making
Data-Driven Planning
Custom ERP offers useful information on business trends and key performance indicators (KPIs). This makes it possible for manufacturers to base their judgments on facts rather than assumptions.
Manufacturers can make smart decisions that promote growth and profitability by examining past data and finding trends.
Better Planning and Forecasts
Success depends on precise production planning and demand forecasts. Manufacturers can plan production schedules, anticipate future demand, and adapt to shifting market conditions with the aid of ERP systems.
By tapping into these benefits of ERP in manufacturing, managers can reduce the danger of inventory shortages or excess inventory and improve their production schedules by utilizing real-time data and sophisticated forecasting tools.
Improved Customer Service
ERP systems assist manufacturers in improving customer service by giving them real-time insights into order progress, stock levels, and delivery dates.
Accurate shipping details, prompt order fulfillment, and effective problem-solving all enhance the client experience and build enduring connections.
Strategic Company Planning
After going through all the benefits of ERP in manufacturing, one thing is clear: custom ERP offers the critical information and understanding required to create winning company plans.
Manufacturers can make well-informed judgments regarding investment, market expansion, and product development objectives by examining historical data and spotting trends.
ERP can assist manufacturers in finding development prospects, allocating resources as efficiently as possible, and enhancing overall company performance.
More Adherence to Compliance and Regulatory Measures
Avoiding expensive fines and penalties by automating compliance inspections and producing reports are some of the most underrated benefits of ERP in manufacturing.
ERP systems can assist manufacturers in adhering to industry standards and regulations, including RoHS, ISO, and FDA.
A Strategic Approach to ERP Integration
Choosing the Appropriate ERP Solution
● Functionality: Your custom ERP should have the modules that support your company-specific activities, including supply chain management, manufacturing, finance, and human resources.
● Scalability: It should be capable of expanding and growing with your company in the future.
● Customization: The ERP system must be customized to your particular business needs.
● Integration Capabilities: Your ERP should easily integrate with external systems.
● Vendor Support: Effective deployment and continuous maintenance depend on strong vendor support.
Integration and Data Migration
After becoming aware of the benefits of ERP in manufacturing, here is how you should deal with your data:
● Ensure Data Quality: Before migration, make sure the data is accurate and comprehensive.
● Perform Data Mapping: Transfer information between the new ERP software and legacy systems.
● Clean your Data: To ensure that it is consistent and standardized.
● Validate your Data: Check for and fix mistakes in the transferred data.
Training Users and Managing Change
● Effective Communication: Ensure all stakeholders understand the benefits of ERP in manufacturing.
● Provide Training: To assist end users in adjusting to the new system, provide them with thorough training.
● Change Management Techniques: Increase adoption and reduce opposition by training your management to work with the digital tools.
● User Adoption: Promote user adoption by offering incentives and continuous assistance.
Getting Over Challenges and Achieving Operational Success
Common Impediments in the Implementation of ERP
Even though the benefits of ERP in manufacturing are quite evident, implementing the solutions in an organization can be challenging. Some of the common impediments include:
● Opposition to Change: Employees may object to modifications to their workflows and work procedures.
● Problems with Data Quality: The ERP system's efficacy may be hampered by poor data quality.
● Complexity of Integration: It can be difficult to integrate the ERP with various other systems.
● Overruns in Cost and Time: ERP deployments can be expensive and time-consuming.
Best Industry Practices
● Unambiguous Business Goals: Clearly state the aims and objectives of the ERP installation.
● Effective Project Management: To supervise the implementation process and assemble an effective project management team.
● Include Important Stakeholders: To guarantee support and buy-in, include important stakeholders from every department.
● Pilot Implementation: To reduce risks and evaluate the framework in a controlled setting, think about using a phased implementation strategy.
● Continuous Improvement: Make sure the ERP is meeting changing business needs by reviewing and optimizing it regularly.
Calculating ERP's ROI
If all the aforementioned benefits of ERP in manufacturing are not convincing enough you should know that in the long term, it offers a significant return on investment. Here’s how you can calculate the ROI of a custom ERP:
● Enhanced Productivity: Calculate the rise in output brought about by fewer manual labor-intensive jobs and more efficient procedures.
● Decreased Costs: Monitor financial gains from reduced operating expenses, better purchasing choices, and decreased inventory levels.
● Increased Customer Satisfaction: Track retention and satisfaction levels.
● Improved Decision-Making: Evaluate how data-driven decision-making affects the operation of the company.
● Faster Time-to-Market: Track how long it takes to create and launch a product.
Conclusion
Manufacturers can improve decision-making, cut expenses, and streamline processes with a custom ERP. It has several advantages, ranging from increased productivity and efficiency to better customer satisfaction and compliance with regulations.
Vestra Inet specializes in creating ERP systems and manufacturing software solutions that are specifically suited to each company's needs. You can maximize the potential of your manufacturing operations with our ERP implementation and integration skills.
To find out more about how realizing the benefits of ERP in manufacturing can assist you in reaching your company objectives, get in touch with us today.