How Manufacturing Process Automation is Shaping the Future of Industries
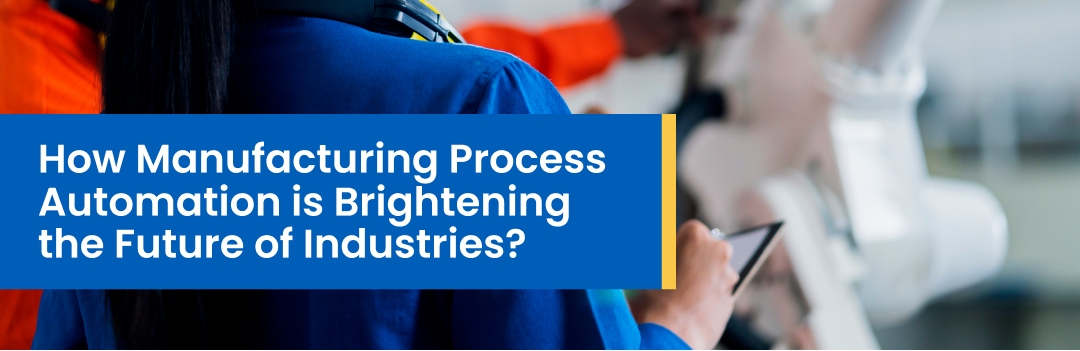
The manufacturing sector is going through a significant transition. New developments in manufacturing process automation are driving the sector into a future with previously unheard-of levels of productivity, agility, and efficiency.
This blog explores the transitional era of industrial advancement from Industry 4.0 to Industry 5.0, examining how innovative technologies such as robotics, artificial intelligence (AI), big data, and the Internet of Things (IoT) are changing how we manufacture goods.
The Ever-Evolving Role of Manufacturing Process Automation
For many years, automation has been crucial to the evolution of manufacturing, replacing monotonous tasks and enhancing human potential. We are currently seeing a new phase of manufacturing process automation driven by cutting-edge technologies.
With increased accuracy and efficiency, smart manufacturing systems are able to execute complicated procedures and surpass simple jobs. Strategic decisions are becoming more and more crucial as automation evolves.
You need a reliable technology infrastructure and access to talented developers with the necessary skill sets to build custom manufacturing software that will make your manufacturing operations more efficient, innovative, and attractive to investors.
Industry 5.0 and The Future of Manufacturing
The next phase of manufacturing process automation, known as Industry 5.0, expands on the framework established by Industry 4.0. In order to create a more sustainable and flexible manufacturing environment, it places a strong emphasis on human-focused collaboration with smart robotics.
Navigating the intricacies of a global marketplace while maintaining a high level of personalization to satisfy ever-evolving customer expectations will require this human-machine cooperation.
Consider a situation in which artificial intelligence (AI) algorithms evaluate real-time sensor data from the manufacturing floor to forecast equipment breakdowns and recommend preventative maintenance measures.
Cobots, (i.e., collaborative robots), help human workers with delicate assembly chores, guaranteeing accuracy and productivity. Industry 5.0's vision of manufacturing process automation encourages a more cooperative and effective workplace.
Emerging Technologies That Are Redefining Manufacturing
Artificial Intelligence
Manufacturing process automation is being revolutionized by AI algorithms. For example, by anticipating possible equipment breakdowns, predictive maintenance tools reduce downtime and increase productivity.
Imagine hundreds of machines in a factory. AI can forecast possible problems with a particular machine by evaluating sensor data and past equipment performance. This enables the scheduling of preventative maintenance, thus reducing the possibility of production delays and expensive downtime.
AI is also being utilized to control quality, with smart systems evaluating camera and sensor data to find flaws early in the manufacturing process. This reduces waste and related expenses in addition to improving product quality.
On a car assembly line, for example, AI-powered vision systems may be used to check goods for even the smallest flaws, guaranteeing that only perfect cars make it to the end.
Smart Robots
Industrial robots are becoming more and more significant as they carry out monotonous, dangerous, and highly precise tasks. Welding robots are capable of working continuously in dangerous settings, handling bulky materials, and welding with unparalleled accuracy.
Furthermore, complex assembly jobs can be programmed into robots, guaranteeing efficiency and uniformity in high-volume manufacturing lines.
The emergence of cobots, or collaborative robots, promotes a safer workplace where people and machines can coexist together. Because of its user-friendly design, Cobots can be easily incorporated into current manufacturing process automation systems.
They can be configured to carry out a variety of duties, including helping with quality control, material handling, and assembly. Thanks to this human-robot partnership, employees can concentrate on more complex jobs that call for creativity, critical thinking, and problem-solving abilities.
Internet of Things
Real-time data gathering and analysis is made possible by the Internet of Things which connects sensors, machines, and devices over a network. Manufacturing process automation, better resource allocation, and problem prediction are all possible with this data.
Smart factories are built on IoT connectivity that enables real-time monitoring and control of the factory floor. Consider a factory where a network of sensors is integrated with the machinery and a production management software.
Pressure, temperature, vibration, and other critical characteristics are all recorded in real-time by the sensors and this data is then used by the software for analysis, adjustments, and quality control. A centralized custom manufacturing software can analyze any changes in data to detect bottlenecks, optimize production workflow, and boost overall efficiency.
Big Data Analytics
Enormous volumes of data produced by networking devices and sensors are extremely valuable for manufacturers because they allow to discover inefficiencies, obtain important insights, and make informed decisions to maximize output by utilizing data analytics approaches.
For instance, manufacturers can forecast probable failures and plan preventative maintenance by examining past data on equipment breakdowns, reducing downtime, and increasing production.
Data analytics can also be utilized to improve quality control, cut manufacturing lead times, and optimize inventory levels.
The Future of Manufacturing: Opportunities and Challenges
Manufacturers have both possibilities and challenges as a result of the use of these novel innovations. Integrating these emerging technologies with the current infrastructure is a major task.
It is also critical to have a trained workforce that can collaborate with the automation equipment and AI software. To upskill their employees and get them ready for the workforce of the future, manufacturers may need to invest in training initiatives.
But there are many advantages for those who accept the change. Manufacturers who engage in manufacturing process automation stand to gain additional flexibility, enhanced productivity, lower expenses, and better product quality.
Conclusion
The developments in manufacturing process automation have opened up a world of opportunities. Manufacturers can build a more productive, sustainable, and flexible sector that prospers in the dynamic global economy by utilizing cutting-edge technology like artificial intelligence (AI), robotics, the Internet of Things (IoT), and big data analytics.
However, the human aspect is still indispensable. Unlocking the full capabilities of this technology transformation will depend on creating an environment of collaboration where intelligent robots and humans work together as we transition to Industry 5.0.
Are you ready to transform your production processes? Vestra Inet provides state-of-the-art custom manufacturing software solutions to assist you in fully utilizing the potential of manufacturing process automation.
Our knowledgeable staff can assist you in putting plans into action that will boost productivity, cut expenses, and enhance the caliber of your output.
To find out how we can assist you in reaching your manufacturing objectives, get in touch with us today and get a free quote.