Lean Manufacturing: Definition, Principles & Implementation Tips
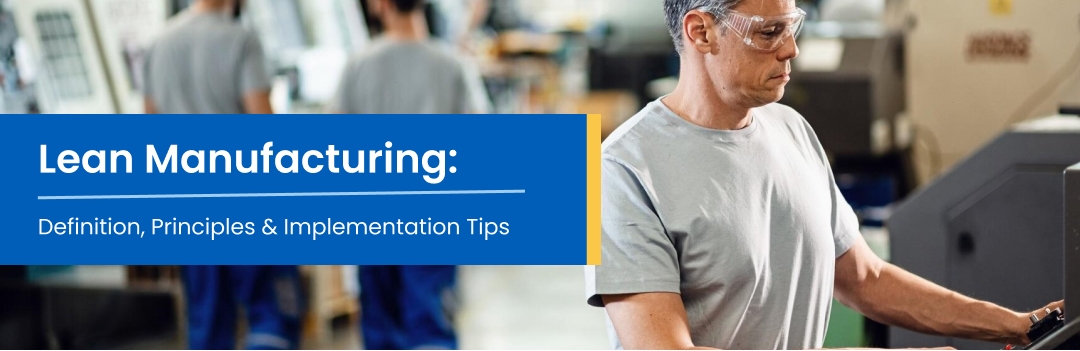
Organizations of all sizes are on a constant quest to improve their efficiency and optimize resource utilization to achieve better results by investing less. Over the years, this exact principle has become a cornerstone of modern manufacturing for companies around the world, acquiring the name of “lean manufacturing”. In this blog, we will explore what lean manufacturing is, cover the five main principles of lean manufacturing and provide tips on how to successfully implement the principles in your business.
What Is Lean Manufacturing?
Lean manufacturing is an approach to streamlining manufacturing operations by optimizing resource utilization, minimizing waste and maximizing value for customers. The approach originated back in the 1950s from the Toyota Production System by Toyota Motor Corporation in Japan. The company was looking to tackle issues of overproduction, inappropriate processing, waiting, transportation, excess inventory, unnecessary motion and defects and created a production system (later given the name of lean manufacturing) which soon was adopted by companies around the world.
Lean manufacturing is based on identifying and eliminating waste, creating streamlined workflow, empowering employees, and continuously improving manufacturing processes with the ultimate goal of becoming more agile, responsive, and competitive in the market. Let’s explore these principles in more detail and understand why they are so important for manufacturing.
What Are Lean Principles In Manufacturing?
Lean manufacturing is based on five principles which include value, the value stream, flow, pull and perfection. Here’s a quick overview of what each principle entails.
1. Value
Value is defined from the perspective of the customer. It is based on what the customer is willing to pay for a product/service and focuses on delivering that product/service with minimal waste.
2. Value stream
The idea of a value stream lies in delivering a product/service while eliminating steps that add no value to the product along the way.
3. Flow
The flow principle is based on the idea of ensuring a continuous flow of work with no delays and interruptions that could potentially compromise the quality of a product/service.
4. Pull
With the pull principle, the work is commenced only when there is demand. This approach is different from the push principle where the production flow is based on the forecasts which are not always accurate.
5. Perfection
This principle ties all the other principles together and is based on the idea of continually improving and perfecting the production process, including eliminating waste, improving quality and increasing efficiency.
Implementing lean manufacturing into your workflow helps safeguard an increase in productivity and efficiency and a reduction in operating costs. Companies that have adopted the lean principles typically see between 20% to 30% cost reduction in the first year post-implementation.
What Are The Instruments For Implementing Lean Manufacturing?
There are various tools and instruments that facilitate the implementation of lean manufacturing in organizations. Here are some of them:
Custom software technologies
Custom software, such as custom inventory management or manufacturing software solutions, are among the most efficient ways to ensure smooth workflow. Inventory and manufacturing process management are indispensable parts of any manufacturing business, so it is essential to make these processes as streamlined as possible.
JIT strategy
Incorporating the JIT (Just-In-Time) strategy in the production workflow can help eliminate waste and improve efficiency. The goal of the JIT strategy is to produce goods only as they are needed, which perfectly aligns with one of the principles of lean manufacturing.
Total Productive Maintenance (TPM)
Implementing a TPM system is another way to succeed in achieving lean manufacturing. TPM is used for maintaining equipment and machinery to prevent breakdowns and downtime. TPM aims to maximize the productivity of equipment and improve overall efficiency.
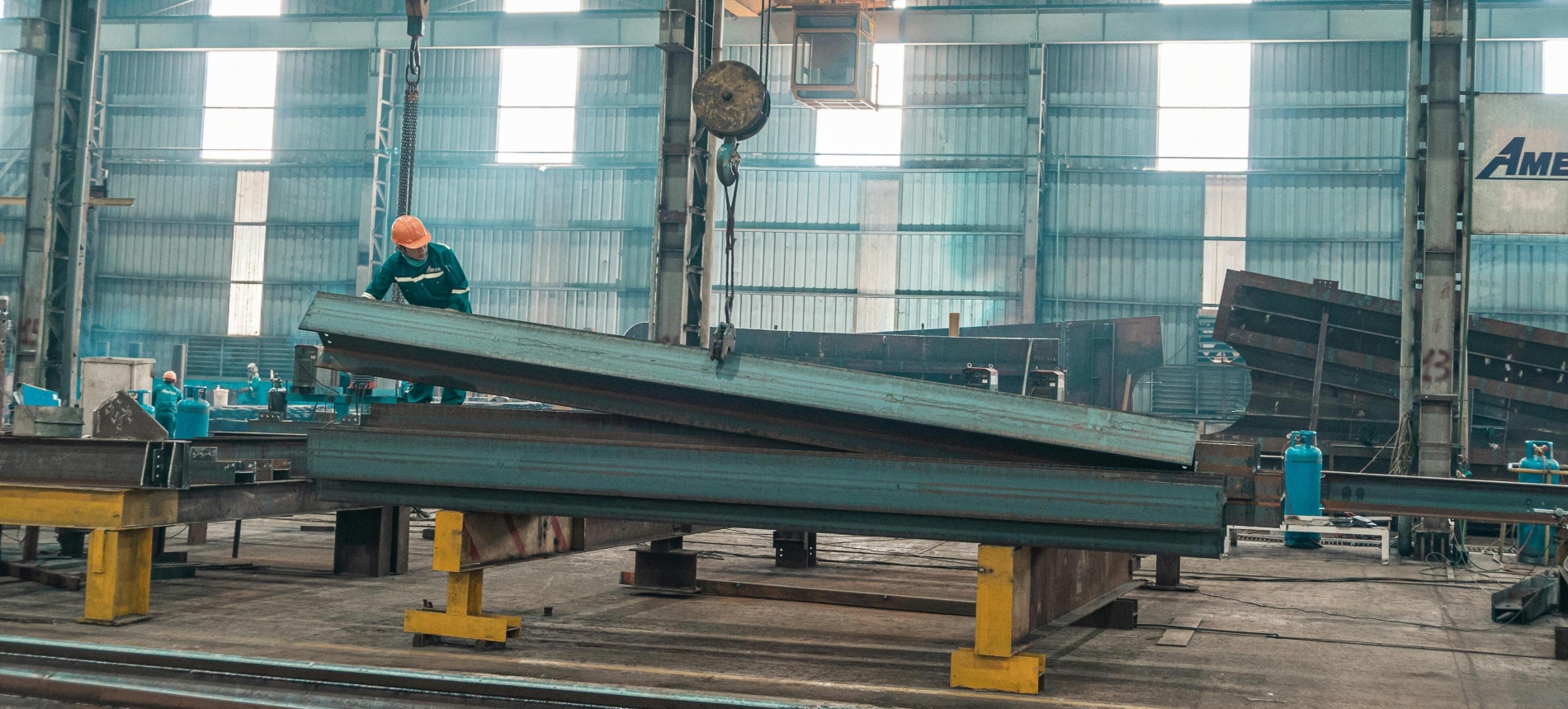
Tips For Successful Implementation of Lean Manufacturing
While lean manufacturing has certainly proven its effectiveness in many industries, one should not underestimate the challenges that come with implementing the principle. Difficulty sustaining improvements, lack of employee buy-in and resource constraints are some of the common challenges organizations face in the implementation of lean manufacturing. Nonetheless, with a proper strategy and execution, implementing lean manufacturing into your workflow can be done with ease. Below are some tips to ensure your implementation of lean manufacturing is a success:
Follow a gradual approach
Start your lean manufacturing implementation by rolling out the principle within a single team. This will help you mitigate the risks associated with the total aversion of the concept across the organization.
Identify value and waste
Identify the activities which add value to the product/service and which waste time and resources in the manufacturing process.
Focus on training and education
Provide comprehensive training on the principles and methodologies of lean manufacturing to your employees to ensure your team is fully prepared for the change.
Prioritize continual improvement
Lean manufacturing is, in a sense, a continuous process with no net result. As such, organizations should strive to continually improve their processes, even after the implementation has successfully been completed. When one organizational problem has been solved, there will always be another to tackle.
Track performance
Performance tracking is one of the key aspects of a successful implementation of lean manufacturing. Establish the KPIs you wish to track and continuously monitor the impact of lean manufacturing on the performance of your business.
Key Takeaways
Lean manufacturing has proven to be a powerful tool for improving the efficiency of the manufacturing process. Yet, lean manufacturing comes with its challenges. To overcome these challenges, organizations should follow a gradual approach to implementing Lean, starting with a single team, and focusing on training and education to ensure employee buy-in. Once the organization has achieved success with its Lean implementation, it is crucial to keep up with the continuous improvement process and improve the areas identified as wasteful.
FAQ
1. What is an example of lean manufacturing?
Lean manufacturing was originally implemented in the automotive industry but soon it was adopted by other industries, too. Today, the principles of lean manufacturing are applied in the manufacturing, aerospace, healthcare, electronics, food and beverage, construction and service industries. Wherever there is a need for process optimization and operating cost reduction, lean manufacturing is a sure way to go.
2. What are the wastes of lean manufacturing?
One of the principles of lean manufacturing is to identify the wastes and eliminate them from the production process as much as it is possible. The common wastes of the production process defined by The Toyota Production System include:
- Excess inventory
- Unnecessary transportation and movement of people, equipment & machinery
- Idling staff or equipment
- Overproduction
- Adding unnecessary features that add no value to the product
- Defects