Production Planning and Control: A Step-by-Step Guide to Achieve Operational Excellence
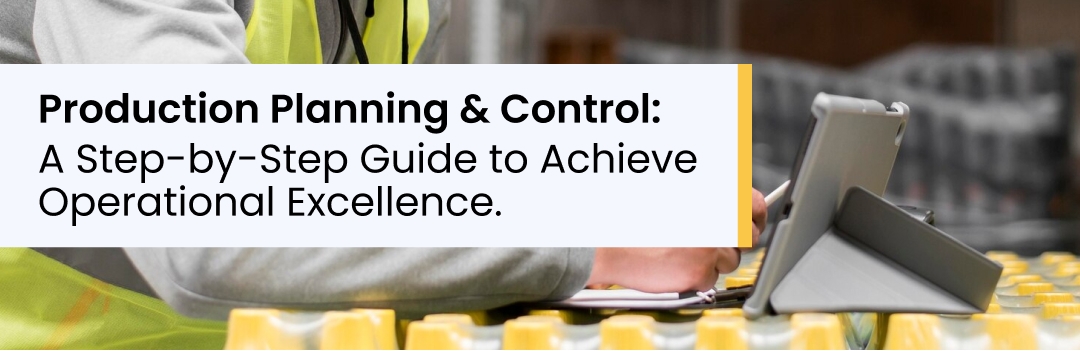
Key Takeaways
1. One of the most important tactics for effective manufacturing operations is production planning and control (PPC).
2. It entails a methodical approach to scheduling, planning, and managing production procedures.
3. Increased client satisfaction, lower expenses, better quality, and increased efficiency are all results of effective PPC.
4. Forecasting demand, production scheduling, capacity planning, material requirements scheduling, dispatching, and control and monitoring are all essential elements of PPC.
5. Blockchain, IoT, ML, and AI are examples of cutting-edge technologies that can further enhance PPC procedures.
6. Ways businesses can use Vestra Inet's custom software services to put PPC strategy into action.
Operating effectively and continuously meeting customer expectations is critical in today's cutthroat manufacturing environment. Production Planning and Control, (PPC for short) is useful in such conditions.
PPC is a thorough approach that guarantees you have the appropriate equipment, personnel, and supplies in a timely manner to fulfill production targets. PPC can boost your bottom line and advance your company by streamlining your production procedures.
What is Production Planning and Control?
A methodical approach to managing every facet of production, from scheduling and planning to execution and monitoring, is called production planning and control.
In essence, it serves as a guide to make sure your production actions complement your overarching business objectives. Below is a summary of the main elements of PPC:
1. Planning: It entails estimating consumer demand, determining the resources needed, and developing a production schedule that details the actions required to meet those needs.
2. Scheduling: This converts the manufacturing plan into a detailed timetable by assigning jobs, materials, and machinery to certain stages.
3. Control: This process entails keeping an eye on the status of production, spotting and resolving any discrepancies in the plan, and adjusting as necessary.
Benefits of PPC Integration for Manufacturers
Your manufacturing operations can gain a lot from putting in place a strong Production Planning and Control system. Some core benefits include:
● Enhanced Production Capacity: By removing bottlenecks and inefficiencies, PPC enables you to make the most of your production facilities, machinery, and workforce.
● Decreased Inventory Costs: You can cut down on surplus stock that ties up precious resources by accurately predicting demand and scheduling your production accordingly.
● On-time Deliveries: PPC guarantees that you have the resources and materials necessary to fulfill production deadlines and provide customers with completed goods on schedule.
● Better Quality Control: PPC can guarantee consistent product quality by including quality control procedures throughout the production process.
● Decreased Waste: Production Planning and Control assists you in maximizing the use of materials and reducing manufacturing waste, which benefits the environment in addition to saving money.
● Improved Decision-Making: PPC offers useful information and insights that can assist you in making well-informed choices regarding resource allocation, production scheduling, and general business strategy.
A Step-by-Step Guide to Production Planning and Control
Manufacturing planning can be overwhelming for many production companies. Nevertheless, it is quite simple to integrate PPC with your existing systems if you follow the step-by-step guide below.
Step-1: Production Planning
Forecasting Consumer Demands: The first stage of production planning and control entails forecasting the demand for your items from future customers. Numerous forecasting methods are available to you, including market trend analysis and historical sales data.
Planning for Sales and Operations (S&OP): This phase is about matching your sales projections with your production plan. In order to ensure that your manufacturing bandwidth can satisfy the expected demand, you will collaborate with your sales staff to compile and analyze their estimates.
Create MPS: Your high-level plan that specifies what goods you will manufacture, in what amounts, and by when is called the Master Production Schedule (MPS). It considers lead times, resource availability, and demand projections.
Work on MRP: The process of identifying the materials, parts, and subassemblies required to manufacture the final products specified in the MPS is known as material requirements planning or MRP. It takes into account things like lead periods for material procurement and the bill of materials (BOM).
Step-2: Routing
Routing outlines the precise order in which a product must be manufactured. It describes how materials move through the manufacturing process and lists the equipment, supplies, and workers needed at each step.
Step-3: Scheduling
Depending on lead times, resource availability, and the routing strategy, scheduling entails giving each production task a set duration. In order to fulfill the overall production deadlines, this guarantees that jobs are finished on schedule and in the right order.
Step-4: Loading
Assigning duties to particular people and machines during loading ensures that the amount of work is distributed evenly and that workers and machines are neither overworked nor idle. This stage of production planning and control aids in resource optimization and bottleneck avoidance.
Step-5: Dispatching
The process of transmitting production orders to the factory floor so that employees can start working on production is known as dispatching. It guarantees that the appropriate supplies, instruments, and machinery are available for every job.
Step-6: Tracking and Controlling Progress
Tracking production progress, spotting plan deviations, and taking the necessary corrective action are all part of monitoring and control. This keeps the production process on course and ensures that quality standards are met.
Best Practices for Manufacturing Planning
● Continuous Improvement: Evaluate and improve production planning and control procedures on a regular basis. Determine what needs to be improved, such as reducing manufacturing lead times, waste reduction, or quality enhancement. Make adjustments and track their effects.
● Collaboration and Interaction: Encourage efficient communication amongst the operations, procurement, sales, and engineering departments that are engaged in the production process. Aligning efforts and preventing misconceptions can be achieved through regular meetings and transparent information exchange.
● Making Decisions Based on Data: Make educated decisions by applying data analytics. To find patterns and areas for improvement, gather and examine data on consumer demand, quality measures, and production performance.
● Adaptability and Flexibility: Be ready to adjust in response to unanticipated interruptions, shifting consumer expectations, and shifting market conditions. Create backup plans and be prepared to modify your production schedules as necessary.
● Standardization: To guarantee efficiency and consistency, use best practices and standardized procedures. This can simplify processes, lower errors, and enhance quality.
Challenges in Production Planning and Control
● Demand Variability: Accurately forecasting and planning output can be challenging when demand fluctuates, resulting in excessive production, insufficient production, and stock imbalances.
● Supply Chain Disruptions: Lead times and material availability can be impacted by supply chain disruptions including supplier delays, transportation problems, or natural catastrophes.
● Resource Constraints: Inadequate labor, equipment, or financial resources might limit flexibility and output potential.
● Quality Control: Problems with quality can result in rework, manufacturing delays, and unhappy customers.
● Technological Difficulties: Complex production planning and control systems may be difficult to implement and manage, and specialized knowledge and continuous assistance are needed.
How Vestra Inet helped a chemical manufacturer by delivering process optimization and custom forecasting solutions
The Client’s Problem
A leading chemical manufacturer approached Vestra Inet with a desire to streamline their manufacturing process through a systematized production planning and control system.
The client needed a system that would optimize their manufacturing process for the best outcomes in addition to forecasting the amount of resin they would need to be producing.
It was inefficient to physically inspect and assign tanks prior to production because the company has many tanks of varying capacities in its facilities in two different locations.
The order in which chemicals are added during manufacture is especially crucial because of the intricacy of working with resins, chemicals, and silicone-based goods. As a result, the client also needed a system that would monitor the proper sequencing of its component items.
Finally, the client needed an efficient method for creating and managing work orders and reports.
Our Solution
We streamlined the client’s manufacturing planning via a production forecasting system. It registers the previous order history of the manufacturing company to predict the amount of a particular product (with 97% accuracy) required to be manufactured and delivered at a set date.
With the help of the production monitoring module in the Production Planning and Control system, the client can accurately allocate the correct facility and tank considering their current work order.
Moreover, the sequencing management feature of the system allows the client to consider previous work orders to figure out the right chemical sequencing.
Thus, the client can supply high-quality resins on time while also streamlining the production process thanks to the combination of the production forecasting system, process automation, and sequence management.
Finally, to enable a quicker and more precise report generation, an enhanced reporting system was built on top of the previously described functionalities.
With the help of production management, sequence management, the forecasting system, and the reporting module, every aspect of manufacturing became highly streamlined and automated, allowing the company to enhance production quality and eliminate delays.
Advanced Manufacturing Planning and Control Techniques
Consider putting these cutting-edge strategies into practice to enhance production planning and control further:
● Lean Manufacturing: An organized method for locating and getting rid of waste in manufacturing operations. Lean manufacturing can greatly increase productivity and cut expenses by concentrating on value-added operations and removing wasteful ones.
● Six Sigma: It is a data-driven approach to process quality improvement and defect reduction. Six Sigma can assist in locating and removing the underlying causes of quality problems by applying statistical methods and problem-solving strategies.
● Theory of Constraints: It is a management concept centered on locating and removing limitations in production systems. TOC can aid in increasing the total system throughput by locating and eliminating the bottleneck.
● Simulation of Discrete Events: A modeling method for simulating and analyzing intricate manufacturing systems is called discrete event simulation. Businesses can find possible bottlenecks, assess the effects of changes, and improve production plans by modeling various scenarios.
The Amazing Future of PPC
The methods and approaches for Production Planning and Control are constantly changing along with technology. The following represent a few of the major PPC trends of the future:
Machine Learning and Artificial Intelligence
● Predictive analytics: By analyzing past data, machine learning and AI algorithms can estimate future demand patterns, allowing for more precise manufacturing planning and forecasting.
● Optimized Scheduling: AI-driven scheduling solutions can reduce downtime and maximize resource allocation, thus boosting productivity.
● Quality Control: AI-powered solutions for quality control can spot flaws and irregularities instantly, guaranteeing the caliber of the final product.
Internet of Things
● Real-time Tracking: IoT sensors can gather information about the operation of machinery, the use of materials, and the status of production, allowing for real-time control and monitoring.
● Predictive Maintenance: IoT is revolutionizing operations software development by evaluating sensor data and anticipating equipment breakdowns, which enables preventive maintenance and reduces downtime in production planning and control.
Digital Twins
● Virtual Tests: By simulating manufacturing processes, digital twins allow for scenario testing and production plan optimization.
● Predictive maintenance: A process of anticipating and proactively addressing possible equipment faults through the analysis of digital twins.
Blockchain
● Logistics Transparency: Blockchain technology can guarantee the legitimacy and caliber of commodities by enabling transparency and traceability across the supply chain.
● Safe Data Exchange: Blockchain technology can make it easier for various supply chain participants to exchange data in a safe and effective manner.
Cloud-based Systems
● Flexibility and Scalability: Cloud-based solutions provide scalability and flexibility, enabling companies to expand their operations and adjust to shifting demands.
● Collaboration and Remote Access: Cloud-based production planning and control solutions facilitate collaboration and remote access, which boosts output and efficiency.
Manufacturers can greatly increase productivity, cut expenses, and boost customer satisfaction by utilizing cutting-edge technologies and properly adopting Production Planning and Control.
Vestra Inet helps companies make data-driven choices, improve resource use, and streamline production processes by understanding their problems and developing a variety of customized production management software and manufacturing planning systems.
You may attain sustainable growth and realize the full potential of your industrial operations with our manufacturing software solutions and expertise. Contact us today at 905-761-8078 to learn more!