Elevating Carlsberg Group's Beer Production with Vestra Inet's Custom Forecasting and Inventory Management Solutions.
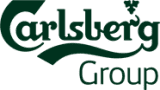
Carlsberg is one of the biggest brewers in the world. Founded in 1847 in Copenhagen, the company brews over 500 drinks and distributes its products across the globe. Carlsberg also has the longest-running partnership in the Premier League with Liverpool FC. They are also credited with the invention of the pH scale, now used by scientists and government organizations globally to measure the acidity of solutions.
- Custom forecasting and analytical software
- Inventory management system with automated purchase order generation
- Customizable reporting
A major brand that incorporates multiple products like Somersby, Kronenbourg 1664, and Tuborg, Carlsberg supplies millions of beverages every day around the world. Furthermore, these multiple brands are brewed and manufactured in different countries across the globe.
Owing to its complex business model, Carlsberg required a tool that can help them accurately predict the amount of beer they needed to produce for everyday consumption. This tool also required to take into consideration important occasions such as sporting events, carnivals, music festivals and more on a regional, national and even global scale. This is paramount from a production standpoint as producing too little will lead to shortage and brewing too much will cause wastage, as beer has an expiration date and is a perishable product.
By automating inventory prediction with the aid of a custom forecasting system, the company can now determine how much stock it requires with greater precision by drawing inferences from past data, with or without variables. With the advent of the forecasting system, the accuracy of the predictions increased from 89 percent to 97 percent.
Furthermore, since the company was also required to procure the aforementioned stock before the date of consumption, the software also had to consider the production timeline for manufacturing the beverage, as brewing beer is a time-consuming process. To add further to the complexity, Carlsberg operates multiple brewing facilities across the world, including Belgium, Germany and Russia, and these breweries make different varieties of beer that have varying production timelines. Thus, depending on the brand and the country it is being brewed and shipped from, the date of production and delivery had to be accurately determined so that the fresh stock can reach the desired location in the right quantities. Moreover, customs and other bureaucratic processes also vary across nations, hence it also had to be taken into consideration as an important variable.
With the aid of extensive inventory management and automated purchase order generation, the orders for a given stock can be placed on time by carefully considering the above-mentioned variables. Thus, it led to achieving impeccable accuracy in terms of quantity, production date and shipping timeline. This level of automation and precision was made possible by performance tracking and reporting systems, which carefully compiled shipping reports and manufacturing data from multiple countries. Thus, this software solution offered complete control over the smallest details of the supply chain of this major conglomerate while also taking out any guesswork from the process.
Manufacturing Management Software
- Full control of production cycle
- Automation of multiple production stages
- 360° view of all production processes
- Flexible scalability
The principal feature of custom-designed production management software is that it is built to adapt to your existing manufacturing processes. It increases the operational efficiency of complex multi-stage production processes by collecting and consolidating data across all units involved in the manufacturing process into one system. Production Management Software allows for centralized control of all manufacturing stages leading to more optimized production flow, saved costs and increased profits. With production management software your work will be smarter, not harder.
Custom Operations Management System
- Custom-made for your business
- Real-time visibility
- Maximizes productivity
- Streamlined workflow
- Performance and productivity monitoring
- Allows businesses to make informed decisions
The primary purpose of operations management systems is to streamline an organization's business processes and improve operational efficiency. By automating repetitive tasks and providing real-time visibility into all aspects of the business, operations systems can help organizations improve workflow, reduce costs, and increase profits.
Operations software can be used to manage a wide range of business operations, including quotation generation, production management, scheduling, inventory control, order processing, shipping and transportation, and much more. A custom operations management system can be tailored to meet the specific needs of any organization and include virtually any feature you may need to streamline your business operations. Operations software is a valuable addition to any business that will help you achieve your goals and improve your bottom line.
Online Ordering System
- Live inventory updates
- Custom price margins
- Quantity discounts
Development and implementation of these online ordering systems leads to seamless end-to-end order placement that significantly improves the ease of the process. Additionally, the elimination of human involvement in the ordering process reduces staffing costs, eradicates the risk of human errors, and makes the ordering systems available 24/7. Special calculator integration also drastically boosts the speed with which large, complex orders are placed and processed. The automation of this system helps reduce supply chain complexity while allowing multi-stage customizations with ease.
Custom Inventory Management Software
- Real-time dashboards
- Automatic conversions of metrics and currencies
- Multiple warehouse management
- Access and tracking of SKUs in all facilities
Every company operates differently in terms of inventory management. While inventory management software applications are available commercially, many of the features are either not applicable for some companies or insufficient for others. Custom inventory management software is designed and tailored to meet your exact specifications. These systems include specialized features for companies, such as compatibility with barcode and QR code scanners, relationships between assemblies with complex part combinations, connectivity to multiple warehouses and databases, real-time updates to stock levels, track using dashboards, dedicated client logins, automatic stock level updates, and more. For businesses that have suppliers in multiple countries, a custom inventory system can help with automated conversions of metrics and currencies, which is useful for uniformity while offering convenience.
Forecasting Software
- Accurate sales and stock level predictions
- Full reporting functionality to provide year-over-year proof of benefits
- Synchronization with key data collection systems for highly accurate predictions
- Analysis of variables and aspects when forecasting
Specialized sales and supply forecasting software is developed to streamline supply chain and logistics management. Complex algorithms support the analysis of multiple data sets to build accurate predictions for supply and demand on a national scale. Items can have a specified minimum stock level in various locations. The system accurately predicts stock levels over a future time period and allows automatic purchase order creation to replenish levels. Additionally, a custom dashboard provides a snapshot of forecasts and gives access to customizable reporting tools.
Performance Tracking and Reporting Systems
- Custom report generation
- Adjustable analysis parameters
- Analyze data from multiple sources
Analysis of performance at all stages including production, sales, shipping, and more is critical to success. Performance tracking systems were designed to specifications and implemented to present detailed analytics data to clients. This data could be automatically recorded over time for multiple variables including process efficiency, sales, cost of production, and more and presented as automatically generated reports. Custom parameters could be set to gather data regarding specific processes.